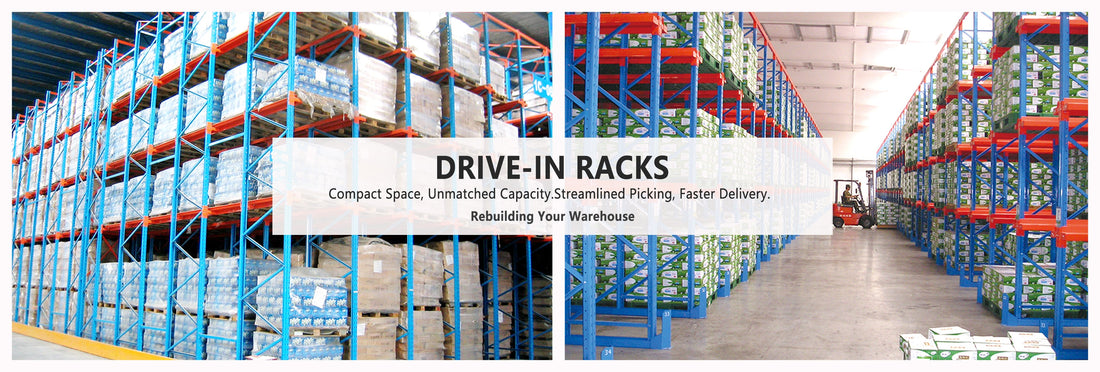
Maximizing Efficiency with Drive-in Racks: Essential Tips for Optimal Warehouse Performance
Share
Jiangsu Satong Intelligent Logistics Equipment Co., Ltd., a leading provider of innovative storage solutions, introduces practical insights for leveraging drive-in racks to enhance warehouse efficiency. Engineered for high-density storage, these systems are ideal for industries prioritizing space optimization and cost-effective operations. Below are key tips to ensure safe, seamless integration of drive-in racks into your logistics strategy.
1. Understand the Basics of Drive-in Racks
A drive-in racking system allows forklifts to directly enter storage lanes, eliminating dedicated aisles and maximizing floor space. Pallets are stored in deep, continuous rows, following a LIFO (Last-In-First-Out) inventory flow. This makes them suitable for:
- Low-turnover goods (e.g., bulk commodities, seasonal items).
- Uniform SKUs with consistent dimensions.
- Full-pallet loads requiring minimal picking.
Satong’s drive-in racks feature CE-certified designs with reinforced steel uprights and electrostatic powder coating, ensuring durability and corrosion resistance.
2. Choose the Right Forklift and Pallet Dimensions
- Forklift Compatibility: Use narrow, agile forklifts to navigate tight lanes. Verify dimensions match the rack’s clearance (e.g., 42-inch width for standard GMA pallets).
- Pallet Standards: Ensure pallets are intact and sized to fit the rack’s rails (40-inch width with 1-inch side clearance). Damaged pallets risk instability and structural damage.
Satong offers customizable drive-in systems compatible with AGV and automated storage technologies for modern warehouses.
3. Optimize Loading and Unloading Processes
- Single-Sided Access: Load from one side for maximum density, or opt for dual-sided drive-through racks for FIFO inventory management.
-
Slow and Steady Operation:
- Raise pallets 1–2 inches above rails before entering lanes.
- Lower loads gently to avoid sudden impacts.
- Use horns and mirrors to alert personnel during entry/exit.
- Depth Control: Limit lane depth to 6–12 pallets to reduce forklift travel distance and collision risks.
4. Prioritize Safety and Maintenance
- Operator Training: Regularly train staff on proper rack entry, load alignment, and emergency protocols.
-
Structural Inspections:
- Check uprights, rails, and welds for wear or damage.
- Reinforce front columns with protective barriers to minimize forklift impacts.
- Weight Compliance: Avoid exceeding the rack’s load capacity (up to 1,500 kg per pallet).
5. Customize for Your Warehouse Needs
Satong’s modular drive-in racks can be tailored to:
- Height & Layout: Adapt to ceiling heights (up to 10 meters) and warehouse configurations.
- Industry Requirements: Add anti-vibration brackets for automotive parts or corrosion-resistant coatings for food storage.
- Automation Integration: Pair with AGVs and IoT sensors for real-time inventory tracking.
Why Choose Satong’s Drive-in Racks?
- Space Efficiency: Store 30% more pallets per square meter compared to traditional systems.
- Global Compliance: ISO 9001 and RoHS certifications ensure international safety standards.
- Sustainability: Collapsible designs reduce shipping waste and energy consumption.
Transform Your Warehouse Today
Contact Satong’s expert team to explore how our drive-in racking solutions can optimize your storage density and operational efficiency. Request a consultation or visit our website to download our catalog.
Contact Satong’s expert team to explore how our drive-in racking solutions can optimize your storage density and operational efficiency. Request a consultation or visit our website to download our catalog.
Keyword: drive-in racking system, high-density storage, forklift safety, pallet dimensions, warehouse efficiency, CE-certified racks, LIFO inventory management